SONOTRONIC GmbH
Becker-Göring-Straße 17-25
76307 Karlsbad, Deutschland
E-Mail: CO2@sonotronic.de
Mo. bis Do. 8:00 – 17:00 Uhr
Freitag 8:00 – 15:00 Uhr
Phone: +49 7248 9166-0
Ultraschall - raffiniert und grandios
Die umweltfreundliche und energieeffiziente Verbindungstechnik
75 % weniger CO2-Emissionen
Die Ultraschall-Technologie ist, im Vergleich zu anderen thermischen Verfahren, schnell, effizient und umweltfreundlich bei der Bearbeitung von thermoplastischen Kunststoffen, Folien und Geweben. Unsere Produkte werden in allen kunststoffverarbeitenden Industrien eingesetzt, zum Beispiel Automobil Interieur und Exterieur, Filtration, Hygiene, technische Textilien, Verpackung, aber auch in der Umwelttechnologie. Mit dem Einsatz von Ultraschall wird im Vergleich zu thermischen Verfahren nur ein Viertel des elektrischen Energiebedarfs für die Produktion benötigt. Die CO₂-Belastung sinkt somit um circa 75 %.
GREEN SONICS die Marke für die zukunftssichere und nachhaltige Ultraschall-Technologie
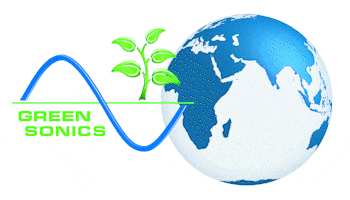
Die Bearbeitung von Kunststoffen mit Ultraschall hat nicht nur Vorteile im Verfahren, sondern ist im Vergleich zur Bearbeitung mit thermischen Verfahren auch deutlich energieeffizienter und umweltfreundlicher. Ultraschall punktet besonders durch den niedrigen Energieverbrauch: Die Energiezufuhr findet nicht durchgängig, sondern nur während der Schweißzeit statt. Der Ultraschall- Schweißprozess selbst ist sehr kurz, wodurch der Energiebedarf ebenfalls gesenkt wird. Außerdem sind die Ultraschall-Werkzeuge während des gesamten Prozesses kalt, das heißt, weder sie noch die Maschine muss aufgewärmt werden.
Um ein dreiviertel sinkt der elektrischen Energiebedarf bei einer Produktion durch den Einsatz von Ultraschall verglichen mit thermischen Verfahren. Darüber hinaus zeichnet sich die Technologie dadurch aus, dass die Ultraschall-Werkzeuge verschleißarm sind und keine Verbrennungsrückstände des Kunststoffs an ihnen haften. Gleichzeitig werden weder Umwelt noch Personen durch schädliche Gase verbrannter Kunststoffe belastet.
Ultraschall vs. Heizstempel vs. Heißluft
Vergleich der drei Nietverfahren
Nieten von Kunststoff-Nietdomen
In einem Testaufbau werden thermoplastische Formteile mit den drei verschiedenen Verfahren Ultraschall, Heißstempel und Heißluft vernietet. Die drei Verfahren werden anhand verschiedener Parameter verglichen.
- Material: PP-GF20
- Abmaße [mm]: D = 8; D = 5,5; H = 8,5
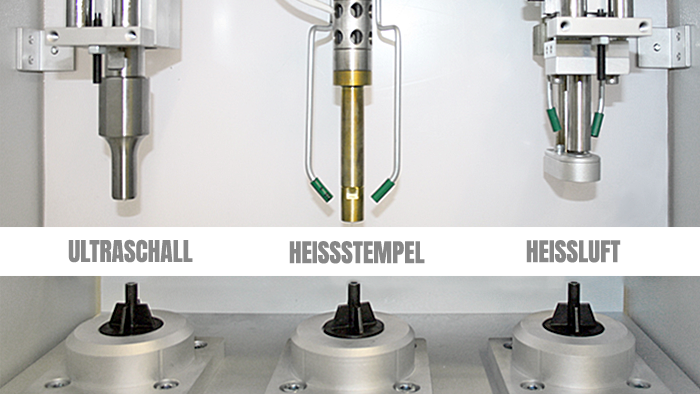
Ultraschall-Nieten
Die Ultraschall-Schwingung erzeugt über das Werkzeug Grenzflächenreibung im Nietdom. Der Nietdom plastifiziert und wird dabei umgeformt.
- Vorschubeinheit in Grundstellung
- Vorschubeinheit in Arbeitsstellung
- Ultraschall ein: 4,5 s
- Ultraschall aus, Haltezeit mit Kühlung ein: 3 s
Heißstempel-Nieten
Das Werkzeug wird elektrisch über eine Heizpatrone erhitzt. Über die Kontaktwärme des Werkzeuges plastifiziert der Nietdom und wird dabei umgeformt.
- Vorschubeinheit in Grundstellung, Nietstempel auf Bearbeitungstemperatur: mehrere Minuten (vor Produktionsbeginn, kontinuierliches Nachheizen notwendig)
- Vorschubeinheit in Arbeitsstellung
- Prägezeit: 12 s
- Haltezeit mit Kühlung ein (Luftstrom auf Heizstempel): 5 s
Heißluft-Nieten
Der Nietdom wird über Heißluft (kontaktlos) erwärmt. Der kalte Nietstempel formt den plastifizierten Nietdom um.
- Vorschubeinheit in Grundstellung, Aufheizen des Systems: 10-15 s (einmalig bei Produktionsbeginn oder längeren Stillstandszeiten)
- Vorschubeinheit in Arbeitsstellung
- Anheizen des Nietdoms: 9-11 s
- Heizen aus, Prägezylinder in Arbeitsstellung zur Formgebung und Kühlung: 3 s
Vergleich*
Ultraschall-Nieten | Heißstempel-Nieten | Heißluft-Nieten | |
Schweißdruck [bar] | 2,5 | 4,0 | 3,5 |
Zykluszeit [s] | 9,5 | 19,0 | 15,0 |
Kühlzeit [s] | 3 | 5 | 3 |
Auszugskraft [N] | 522 | 486 | 933 |
Energiebedarf/ Zyklus [Wh] |
0,1 | 1,9 | 3,3 |
Luftverbrauch/ Zyklus [l/min] |
15 | 25 | 35 |
Fazit
- Bei denselben Versuchsbedingungen weist Ultraschall-Nieten die besten Ergebnisse auf:
- Niedrigster Energieverbrauch (deutlich)
- Kürzeste Zykluszeiten
- Hohe Zugfestigkeit
- Auch in Anforderungen wie Prozess-Sicherheit und Prozess-Überwachung ist das Ultraschall-Nieten den beiden anderen Verfahren überlegen.
- Ultraschall-Nieten eignet sich auch zum Nieten von tief liegenden oder an senkrechten Wandungen platzierten Nietpins.
- Die Mehrkosten von Anlagen mit Ultraschall-Technologie (ca. 5 bis 8 %) amortisieren sich schnell durch Einsparungen im Energiebedarf und in der Prozesszeit.
- Ultraschall-Technologie ermöglicht eine Kombination von mehreren Anwendungen in einer Anlage: z.B. Nieten, Schweißen, Schneiden und Stanzen.